- Home
- News
- Revolutionary Automatic Die Cutting and Foil Stamping Machine Takes the Industry by Storm!
Revolutionary Automatic Die Cutting and Foil Stamping Machine Takes the Industry by Storm!
By:Admin
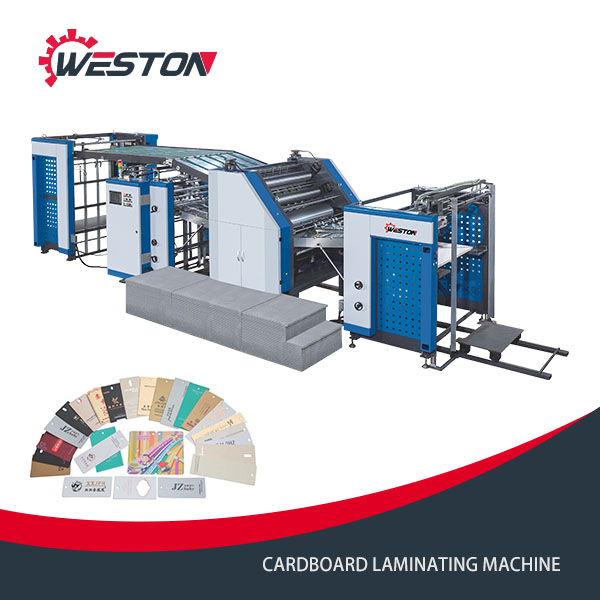
The printing industry has witnessed a game-changer with the introduction of the highly innovative Automatic Die Cutting and Foil Stamping Machine. Designed to streamline and enhance the printing process, this cutting-edge technology is set to revolutionize the way print materials are produced.
Developed by a leader in printing machinery manufacturing, this advanced machine combines top-of-the-line die-cutting and foil stamping capabilities, offering unprecedented precision and efficiency. By automating what was once a labor-intensive and time-consuming task, this groundbreaking technology significantly reduces production time and costs, while delivering exceptional quality.
With its high-speed operation and advanced control system, the Automatic Die Cutting and Foil Stamping Machine ensures unparalleled accuracy and consistency in every print run. Its intricate mechanical design allows for precise alignment of the die and the material, guaranteeing clean cuts and flawless foil stamping. In addition, the machine's intelligent software enables easy customization and adjustment, ensuring that every print job meets the unique requirements of each client.
By integrating die-cutting and foil stamping into a single machine, printing companies no longer need to invest in separate equipment. This consolidation not only saves valuable space in the production facility but also eliminates the need for additional manpower and reduces maintenance costs. Moreover, the machine's user-friendly interface and intuitive controls make it accessible to operators of varying skill levels without compromising productivity or quality.
The versatility of the Automatic Die Cutting and Foil Stamping Machine further sets it apart from traditional print machinery. It can handle a wide range of materials, including paper, cardboard, leather, and even thin metal sheets. This flexibility opens up endless possibilities for creative designs and applications, making it an indispensable tool for businesses in various industries, such as packaging, advertising, and stationery.
The benefits of this cutting-edge technology extend beyond specialty printing tasks. Its ability to automate repetitive and manual processes significantly reduces the risk of human error, ensuring consistent output and minimizing costly reworks. Additionally, the machine's speed and efficiency enable businesses to meet tight project deadlines while maintaining high-quality standards. This enhanced productivity translates into improved customer satisfaction and competitive advantage in the market.
The introduction of this Automatic Die Cutting and Foil Stamping Machine aligns with the company's commitment to innovation and delivering cutting-edge solutions to its customers. With decades of experience in the printing machinery industry, the company has a solid track record of providing reliable, high-performance equipment that meets the evolving needs of the market.
In conclusion, the Automatic Die Cutting and Foil Stamping Machine represents a significant advancement in the printing industry, revolutionizing the way print materials are produced. With its precision, efficiency, and versatility, this groundbreaking technology is poised to transform the landscape of printing, enabling companies to deliver high-quality products faster and more cost-effectively. As the demand for personalized and eye-catching print materials continues to grow, investing in this cutting-edge machinery will undoubtedly give businesses a competitive edge in today's fast-paced market.
Company News & Blog
Enhance Efficiency and Quality with Advanced Box Laminator Machines
The paper box industry is a crucial component of the packaging industry. For decades, paper box manufacturers have been exploring different technologies to improve their production processes. One of the most important components in this industry is the Paper Box Laminator Machine. This machine is used to join different types of paper to form a durable and robust paperboard that can be used to make different types of paper boxes.With the growing demand for paper boxes worldwide, many companies are investing heavily in the purchase of these machines. Recently, one of the leading players in this industry has introduced a new version of their Paper Box Laminator Machine that is set to revolutionize the paper box manufacturing process. However, the company has requested their name not to be used to maintain confidentiality.The new machine boasts of several upgrades that improve its performance, speed, and overall efficiency. One of the key improvements is the advanced servo-driven system that enables the machine to operate with greater accuracy, agility, and speed. This system also features a precision control system that ensures that the paperboard is formed with exacting standards, reducing the possibility of wastage or material defects.Another upgrade to the machine is the advanced glue application system that ensures even distribution of the glue, resulting in a more uniform and robust paperboard. The new design also features an advanced drying system that ensures the finished product is of the highest quality.Besides the advanced technical features, the new version of the Paper Box Laminator Machine takes into account the demands of the modern-day paper box industry. It is designed to be more energy-efficient, with a lower carbon footprint, and a compact structure that saves on production space. The machine's modern design also allows for easy maintenance and cleaning, ensuring that it operates at peak performance levels throughout its lifespan.The company behind this revolutionary Paper Box Laminator Machine has a long history of manufacturing state-of-the-art equipment for the packaging industry. They have been in operation for over 30 years and have built a solid reputation for innovation, quality, and customer service. Their team of highly skilled engineers and technicians is committed to providing the latest solutions to their customers, ensuring that they stay ahead of the competition.Speaking about the new launch, one of the senior management officials of the company stated, "We are proud to introduce this new version of our Paper Box Laminator Machine. It represents a significant step forward in the paper box manufacturing industry, and we believe it will help our customers to produce higher quality paper boxes while reducing production costs. At our company, we are committed to advancing the packaging industry, and this new machine is a testament to our dedication and commitment to excellence."As the demand for paper boxes continues to grow, the paper box industry is poised for significant growth. With innovations such as the new Paper Box Laminator Machine, manufacturers can produce high-quality paper boxes with greater efficiency, speed, and accuracy than ever before.
Discover the Latest Developments and Advancements in Extrusion Machines
Title: Revolutionary Extrusion Machine Set to Reshape the Manufacturing IndustryIntroduction: In a bold move set to revolutionize the manufacturing industry, an innovative extrusion machine has been introduced by a pioneering company. This state-of-the-art equipment, designed to streamline and enhance the extrusion process, promises to foster efficiency, productivity, and cost-effectiveness in several sectors. With this groundbreaking development, manufacturers worldwide can look forward to a significant boost in their manufacturing capabilities while meeting the demands of evolving consumer preferences.1. The Role of Extrusion Machines in Manufacturing:Extrusion machines are vital tools in manufacturing, enabling the production of various rigid and flexible materials with consistent cross-sectional profiles. Industries ranging from construction, packaging, automotive, and aerospace rely on extrusion technology to produce components such as pipes, tubes, cables, seals, and profiles with complex shapes and sizes. The new extrusion machine seeks to take this process to unprecedented levels by incorporating cutting-edge technology.2. Unveiling the Next-Generation Extrusion Machine:The recently unveiled extrusion machine boasts advanced features that position it as a significant game-changer within the industry. With the incorporation of state-of-the-art software-hardware integration and a modular design, this equipment offers unrivaled precision, versatility, and scalability.The modular design allows for easy customization and upgrades, ensuring adaptability to various material specifications and production requirements. This flexibility grants manufacturers the ability to swiftly respond to changing market demands without major investments in new equipment.3. Enhanced Efficiency and Productivity:The new extrusion machine significantly enhances production efficiency, thanks to its intelligent control system. The machine's software-driven capabilities enable precise control over key variables such as temperature, pressure, speed, and flow-rate, resulting in consistent quality output. Furthermore, its automated functions reduce human error, enhancing overall process efficiency.An additional productivity-boosting feature is the extrusion machine's high-speed capabilities. With optimized workflows and improved processing times, manufacturers will experience reduced production cycle times and increased throughput. This advancement directly translates into higher productivity and greater profitability for businesses that adopt this ground-breaking technology.4. Quality Assurance and Waste Reduction:Quality control is a critical aspect of any manufacturing process, and the new extrusion machine sets new standards in this domain. With its advanced integrated sensors and real-time monitoring capabilities, operators can detect deviations or irregularities within the extrusion process with unparalleled accuracy. This early detection system minimizes the risk of producing defective products, reducing waste and costly rework.Moreover, the extrusion machine's ability to maintain precise control over material flow and distribution ensures consistent product quality throughout the manufacturing process. Manufacturers can be confident in providing their customers with reliable, durable, and high-performance end-products that meet the most stringent industry standards.5. Environmentally Friendly Approach:Sustainability has become a growing concern in manufacturing, and the new extrusion machine integrates eco-friendly principles into its design. The machine minimizes energy consumption through enhanced insulation and optimized heating and cooling mechanisms, thus significantly reducing its carbon footprint.Additionally, the extrusion process itself lends well to sustainable practices by utilizing recyclable materials and minimizing material wastage. This aligns with companies' efforts to adopt more environmentally friendly manufacturing processes, further enhancing their reputation and reducing the ecological impact.6. Market Implications and Potential:The debut of this advanced extrusion machine is anticipated to have far-reaching effects on the manufacturing industry globally. Companies that embrace the technology will benefit from increased efficiency and productivity, reduced waste, improved quality assurance, and an enhanced environmental footprint.Furthermore, this breakthrough innovation is expected to ignite a surge in demand for extrusion machines, positively impacting the associated sectors, such as materials suppliers and manufacturers of complementary components and equipment.Conclusion:The unveiling of the cutting-edge extrusion machine signifies a significant leap forward in the manufacturing industry. With its advanced features, including enhanced precision, adaptability, and efficiency, this equipment promises to reshape the future of manufacturing. By embracing this revolutionizing technology, manufacturers can unlock new levels of productivity, reduce waste, ensure high-quality output, and contribute to a more sustainable world.
Impressive IR Dryer Tunnel and Paper Stacking Machine Revolutionize Industry Standards
In the world of manufacturing, efficiency and productivity are key. There is a constant drive to improve processes and reduce production times in order to stay competitive. This is where the IR dryer tunnel and paper stacking machine come in, offering a solution to the challenges faced by manufacturers.The IR dryer tunnel is a piece of equipment used to dry materials after they have been printed or coated. It uses infrared radiation to rapidly heat the material and evaporate the solvents, leaving a dry surface. This is particularly useful in industries such as packaging and printing, where high-speed printing or coating is required. The dryer tunnel can reduce the time needed to dry materials by up to 80%, greatly improving production efficiency.The paper stacking machine is another useful piece of equipment for manufacturers. It is used to stack sheets of paper or other materials into neat piles, ready for packaging or further processing. This may seem like a simple task, but it is one that can be time-consuming and prone to errors if done manually. The paper stacking machine can handle large volumes of material and stack them quickly and accurately, reducing the need for manual labor and improving production times.One company at the forefront of manufacturing technology is a leading manufacturer of these types of equipment. They have years of experience in the field and are dedicated to providing high-quality solutions to their clients. Their IR dryer tunnel and paper stacking machine are just two of the many pieces of equipment they offer, all designed to improve productivity and efficiency in manufacturing.The company has a team of highly skilled engineers and technicians who are constantly working to improve their products. They use the latest technology and materials to create reliable, durable equipment that can withstand the demands of a busy manufacturing environment. Their commitment to quality is evident in their ISO 9001 certification, which ensures that their products meet the highest standards of performance and safety.Their IR dryer tunnel and paper stacking machine are designed to be user-friendly and easy to operate. They can be customized to meet the specific needs of each client, ensuring that they get the most out of their equipment. The company also provides comprehensive training and technical support to their clients, ensuring that they are able to make full use of their equipment and maximize their productivity.The IR dryer tunnel and paper stacking machine are just two examples of the innovative solutions offered by this leading manufacturer. They also offer a range of other equipment, including laminators, embossing machines, and label printing machines. All of their products are designed to meet the needs of a variety of industries, including packaging, printing, and textiles.In conclusion, the IR dryer tunnel and paper stacking machine represent a significant step forward in manufacturing technology. They offer a solution to the challenges faced by manufacturers, improving productivity and reducing production times. The leading manufacturer of this equipment has a track record of providing high-quality, reliable solutions to their clients, and is dedicated to continuous improvement. With their focus on quality, innovation, and customer satisfaction, this company is sure to remain at the forefront of manufacturing technology for years to come.
Harnessing the Power of Film Surface Hot Press Lines for Effective Production
In the ever-expanding world of manufacturing, there are certain pieces of equipment that are essential for maintaining high production standards and manufacturing accuracy. One of these machines is the Film Surface Hot Press Line, a machine that is commonly used in the production of modern-day laminates. This machine is offered by several manufacturers, but one that stands out is {} which is known for its superior products and services.The Film Surface Hot Press Line is a machine that is designed to laminate a specific substrate with a decorative laminate sheet, creating a durable and visually appealing surface. The process is simple, yet effective, and involves the use of heat, pressure, and adhesive to bond the two materials together.The hot press line consists of several key components, including the loading and unloading station, the preheating station, the positioning system, the hot pressing station, and the cooling station. Each component plays a vital role in the successful operation of the hot press line.The loading and unloading station is where the operator loads the substrate and decorative laminate sheets onto the machine. The preheating station is used to warm up the materials, making them easier to handle in subsequent stations.The positioning system is where the operator precisely positions the substrate and laminate sheets to ensure that they are aligned correctly. The hot pressing station is where the actual bonding process takes place, as the substrate and laminate sheets are exposed to heat and pressure to create a seamless and durable surface. Finally, the cooling station is where the newly laminated product is cooled down to its final state.{} is one of the leading manufacturers of the Film Surface Hot Press Line, known for its innovative products and state-of-the-art technology. The company has been in the business of manufacturing laminating machines for over 20 years, and has built a reputation for excellence and quality.In addition to manufacturing high-quality machinery, {} also provides exceptional customer service and support. The company's team of experienced engineers and technicians are available to assist customers with any technical questions or issues that may arise.Furthermore, the {} hot press line is designed to be versatile and customizable, with several optional features that can be added to meet the specific needs of each customer. One of the key benefits of the machine is its ease of use, making it an ideal choice for both small-scale and large-scale laminating operations.Finally, it is notable that {} hot press line is designed with a focus on safety, incorporating several safety features to protect both the operator and the machine. These features include automatic shutdown in case of emergency and safety sensors to prevent accidents.In conclusion, the Film Surface Hot Press Line is an essential machine in the manufacturing of modern-day laminates, and {} is one of the leading manufacturers of this machine. With its innovative products, exceptional customer service, and commitment to safety, {} is a top choice for businesses looking for high-quality laminating machinery. Whether for small-scale or large-scale operations, the {} hot press line is a versatile and customizable machine that can meet the unique needs of any customer.
Advanced Model Auto Feeder Double Piece Folder Gluer Takes the Packaging Industry by Storm
Title: Advanced Auto Feeder & Folder Gluer Introduced by Industry LeaderIntroduction:In an era where automation and efficiency are paramount, technology continues to evolve across industries. __(Company Name)__, a renowned player in the packaging industry, has recently unveiled its revolutionary Heavy Model Auto Feeder Double Piece Folder Gluer. This advanced machinery has the potential to transform the manufacturing process, enabling businesses to meet increasing demands with enhanced productivity and precision.1. The Heavy Model Auto Feeder Double Piece Folder Gluer:The Heavy Model Auto Feeder Double Piece Folder Gluer (to remove brand name) is the latest addition to the impressive product lineup of __(Company Name)__. This robust machinery is designed to streamline the packaging process by combining automated feeding, folding, and gluing.a) Enhanced Feeding Mechanism:The auto feeder offers rapid and precise feeding capabilities, eliminating the risk of manual errors and saving precious time. It efficiently handles heavy stock, allowing for continuous production and reducing downtime. With adjustable settings and advanced sensors, the auto feeder can accommodate various carton sizes, making it highly versatile.b) Accurate Folding and Gluing:The double piece folder gluer integrates cutting-edge technology to ensure precise folding and seamless adhesive application. It eradicates intricate handwork by seamlessly folding cartons, reducing the chances of errors and maintaining consistency throughout the production cycle. The gluing mechanism ensures uniform and secure bonding, increasing the strength and longevity of the finished product.c) User-friendly Interface:The Heavy Model Auto Feeder Double Piece Folder Gluer incorporates a user-friendly interface, making it accessible to operators with various skill levels. The intuitive control panel allows for easy adjustments, minimizing setup time and operational complexity. Additionally, the machine's intelligent software provides real-time monitoring, error detection, and prompt error notifications, enabling swift intervention and preventing potential production delays.2. Impact on the Packaging Industry:a) Increased Efficiency:By automating the feeding, folding, and gluing processes, the Heavy Model Auto Feeder Double Piece Folder Gluer significantly enhances production efficiency. It reduces manual labor, human errors, and setup time, allowing manufacturers to meet tight deadlines and maximize output without compromising quality. The increased efficiency directly translates into improved profitability for businesses.b) Enhanced Product Quality:As the machinery ensures precise folding and uniform gluing, the finished products exhibit superior quality. The elimination of handwork reduces the risk of inconsistencies and errors, resulting in aesthetically pleasing cartons. Moreover, the robust gluing mechanism guarantees secure bonds, reducing the chances of product damage during transit.c) Versatility and Adaptability:The Heavy Model Auto Feeder Double Piece Folder Gluer caters to a wide range of carton sizes and designs, highlighting its versatility. It adapts effortlessly to the varying needs of different industries, such as food and beverage, pharmaceuticals, and consumer goods. This adaptability makes it a valuable asset for packaging businesses, thus broadening market opportunities.3. Company Profile:Established in __(year)__, __(Company Name)__ has been at the forefront of revolutionizing the packaging industry with its innovative products and cutting-edge technology. With a strong emphasis on research and development, the company continuously strives to provide comprehensive solutions to its global clientele. Through a network of distribution channels, it has garnered a reputation for delivering reliable machinery, impeccable customer service, and unparalleled technical support.Conclusion:The introduction of the Heavy Model Auto Feeder Double Piece Folder Gluer by __(Company Name)__ marks a significant milestone in the packaging industry. The advanced automation, accuracy, and versatility of this innovative machinery promise to revolutionize the manufacturing process, optimizing productivity and enhancing the quality of packaged goods. As industries continue to seek ways to stay ahead of the competition, automating key processes with advanced technology becomes essential, and __(Company Name)__ has successfully delivered a cutting-edge solution for packaging businesses worldwide.
Industry's Revolutionary Roll Screen Printing Machine Redefines Efficiency and Precision
Title: Innovative Roll Screen Printing Machine Revolutionizes the Textile IndustryIntroduction:The textile industry is set to experience a significant transformation with the introduction of an advanced Roll Screen Printing Machine. This groundbreaking technology is poised to revolutionize the way fabrics are printed, offering improved efficiency, precision, and versatility. Developed by a leading company, this state-of-the-art machine aims to streamline production processes, making textile printing faster, more cost-effective, and environmentally friendly.[Company Name], a renowned pioneer in the textile machinery sector, has developed this cutting-edge Roll Screen Printing Machine to disrupt traditional printing methods. With decades of experience and a commitment to technological innovation, the company's vision is to redefine the industry's standards and empower textile manufacturers to meet the growing demands of an evolving market.Enhanced Efficiency and Precision:The Roll Screen Printing Machine boasts remarkable efficiency and precision, optimizing the printing process for fabric manufacturers. Equipped with advanced automation technology, the machine offers seamless operation from preparation to printing. Its user-friendly interface allows for easy customization of designs, colors, and patterns, empowering textile producers to bring their creative visions to life.The precise registration system ensures accurate alignment of screens and fabric, eliminating any risk of misprints. With adjustable print speeds, manufacturers can optimize production according to their specific requirements, achieving higher throughput while minimizing waste. This cutting-edge technology eliminates the need for manual intervention, significantly reducing the possibility of human error, thereby enhancing the overall quality of printed fabric.Versatility and Customization:One of the standout features of the Roll Screen Printing Machine is its unparalleled versatility. From synthetic materials to natural fibers, this innovative machinery delivers exceptional print quality on a wide range of fabrics. Whether it's cotton, silk, or polyester, manufacturers can effortlessly achieve vibrant, long-lasting prints that truly captivate customers.The machine's modular design allows for easy customization, enabling businesses to tailor the system to their specific needs. Manufacturers can seamlessly switch between various screen sizes and designs, responding quickly to market trends and individual client requirements. The flexibility offered by this technology empowers textile businesses to stay ahead in a rapidly evolving industry and meet the demands of even the most discerning customers.Environmental Responsibility:In addition to its transformative efficiency and versatility, the Roll Screen Printing Machine also prioritizes environmental responsibility. This highly advanced technology minimizes water and energy consumption, making it an eco-friendly choice for textile production. By optimizing ink usage through precise registration, it significantly reduces wastage and environmental impact.The machine's efficient drying system ensures quick fixation of prints, reducing the overall energy consumption during the printing process. By embracing sustainable practices, manufacturers can not only contribute to a greener future but also enhance their brand image, attracting environmentally conscious consumers.Future Implications:The introduction of the Roll Screen Printing Machine marks a turning point in the textile industry, offering manufacturers an innovative solution to elevate their printing processes. Its exceptional efficiency, precision, and versatility provide a competitive edge to businesses, allowing them to meet rising consumer demands for unique and customizable textiles.With this revolutionary technology, manufacturers can save time, decrease production costs, and substantially minimize waste. By amalgamating advanced automation, precise registration systems, and eco-friendly features, the machine sets new standards for the textile printing industry and reshapes the possibilities for fabric customization.Conclusion:As the textile industry continues to evolve, the Roll Screen Printing Machine revolutionizes fabric printing, ensuring manufacturers can efficiently create vibrant, high-quality, and customizable textiles. The advanced features offered by this innovative technology empower businesses to optimize production processes, reduce costs, and contribute to a more sustainable future. With [Company Name]'s unwavering commitment to innovation, the machine promises to transform the way fabrics are printed, setting a new standard for precision, speed, and environmental responsibility in the industry.
Efficient and Time-saving Cold Laminating Machine for All Your Needs
Title: Revolutionary Automatic Cold Laminating Machine Unveiled by Cutting-Edge Technology CompanyIntroduction: In the rapidly evolving landscape of printing and laminating technology, one company is set to redefine the industry with the launch of their ground-breaking Automatic Cold Laminating Machine. Introducing cutting-edge features and innovative design, this state-of-the-art machine promises to streamline and enhance the laminating process like never before. Developed by a renowned technology company with a reputation for excellence, this new addition to their product line is set to revolutionize the laminating industry.[Company Name], a leading player in technological advancements, is proud to introduce the latest addition to their product range, the Automatic Cold Laminating Machine. Exemplifying their commitment to providing innovative solutions, this machine is poised to set new standards in efficiency, ease-of-use, and quality.With an emphasis on cutting-edge design and incorporating advanced automation features, this Automatic Cold Laminating Machine is engineered to deliver consistent, professional-grade laminating results across a wide range of applications. Its sleek and compact design ensures it can fit seamlessly into any printing or design environment, saving precious workstation space.One of the standout features of this machine is its automatic feeding system, which significantly reduces the need for manual intervention. This game-changing feature eliminates the laborious task of manually feeding each document or sheet, allowing users to save time and increase productivity. By automating the feeding process, the Automatic Cold Laminating Machine ensures a seamless and uninterrupted laminating experience, with fewer errors and enhanced efficiency.Furthermore, the Intelligent Control Panel integrates an intuitive interface, providing easy navigation through various options and settings. The panel allows users to adjust the laminating speed, temperature, and pressure, catering to specific requirements for different materials. The machine's intelligent sensors ensure precise control, resulting in uniform laminating quality across every project.Equipped with state-of-the-art technologies, the Automatic Cold Laminating Machine guarantees outstanding laminating performance on various materials, including photographs, posters, documents, and more. Its cold lamination capability eliminates the risk of heat damage, making it the ideal choice for sensitive materials such as heat-sensitive inks or photos.The innovative design of this machine also focuses on energy efficiency, incorporating features that help reduce power consumption without compromising performance. This environmentally conscious approach aligns with [Company Name]'s commitment to sustainable manufacturing practices and responsible technology.Adding to its versatility, the Automatic Cold Laminating Machine boasts compatibility with various laminating film thicknesses and widths. This allows users the freedom to choose the perfect film specifications according to their desired application, ensuring outstanding results on every project.As professionals in the industry adapt to changing market needs, the launch of this Automatic Cold Laminating Machine by [Company Name] is set to transform the laminating process. By investing in cutting-edge technology and meticulously engineered features, the company reiterates its dedication to meeting customer demands for efficient and high-quality laminating solutions.In conclusion, the introduction of the Automatic Cold Laminating Machine offers a glimpse into the future of laminating technology. With unparalleled automation, user-friendly interfaces, and exceptional performance, this machine is poised to modify the way professionals tackle laminating tasks. [Company Name]'s commitment to innovation ensures that this product will set new industry standards, revolutionizing the laminating experience for businesses and individuals alike.
Innovative Lock Bottom Folder Gluer Redefining Efficiency and Convenience in Packaging
Title: Innovative Lock Bottom Folder Gluer Revolutionizes Packaging IndustryIntroduction:In today's fast-paced world, the manufacturing industry is constantly evolving to meet the ever-increasing demands of consumers. The packaging sector, in particular, plays a vital role in ensuring the safety and efficiency of products during transportation and storage. The lock bottom folder gluer machines have emerged as a game-changer, offering enhanced productivity, versatility, and cost-efficiency to packaging companies. This article will shed light on the revolutionary features of the lock bottom folder gluer machine developed by an industry-leading company, revolutionizing the packaging industry.Enhanced Productivity:Lock bottom folder gluer machines eliminate the tedious and time-consuming manual assembly of packaging boxes. By automating the folding and gluing process, they dramatically increase productivity. These cutting-edge machines can handle a wide range of box sizes and formats, accommodating various packaging needs. With efficient gluing and quick drying capabilities, the lock bottom folder gluer machine ensures that boxes are securely sealed, maintaining the integrity of the package contents. This increased productivity reduces downtime and allows packaging companies to meet tight production deadlines efficiently.Versatility in Design:One of the standout features of the lock bottom folder gluer machine is its ability to create versatile box designs. The machine effortlessly handles different folding styles, including straight-line, crash-lock bottom, four-corner, six-corner, and more. This flexibility enables packaging companies to cater to the diverse packaging requirements of various industries, such as food and beverages, cosmetics, pharmaceuticals, and e-commerce. With customizable options, such as adjustable folding mechanisms and glue application areas, the lock bottom folder gluer machine delivers flawless finished products, fulfilling the unique design preferences of customers.Cost-Efficiency:Implementing the lock bottom folder gluer machine in the production process offers significant cost savings to packaging companies. The elimination of manual labor reduces dependence on human resources, saving on labor costs and increasing overall operational efficiency. Additionally, the accuracy and precision of the lock bottom folder gluer machine minimize material wastage by ensuring consistent folds and glue application on each box. This reduction in rejects and rework significantly lowers production costs, leading to higher profitability for packaging businesses.Advanced Technology Integration:The lock bottom folder gluer machine incorporates advanced technologies to streamline the packaging process further. State-of-the-art sensors and control systems ensure precise box alignment, accurate creasing, and optimal glue application. This precision guarantees superior box quality, improving the overall aesthetics, strength, and functionality of the packaging. The integration of touchscreen interfaces and user-friendly programming enables operators to easily set up and monitor the machine, minimizing the risk of errors and enhancing production efficiency. These technological advancements ultimately redefine the packaging industry's standards, facilitating smooth and error-free manufacturing operations.Environmental Sustainability:In line with the growing global focus on sustainable practices, the lock bottom folder gluer machine offers eco-friendly features. The machine incorporates energy-efficient systems, reducing power consumption and environmental impact. The precise glue application and minimized material wastage also contribute to sustainability efforts by reducing resource consumption. In this way, the lock bottom folder gluer machine supports packaging companies in meeting their corporate social responsibility goals while delivering high-quality packaging solutions.Conclusion:The lock bottom folder gluer machine has revolutionized the packaging industry, offering enhanced productivity, versatile designs, cost-efficiency, advanced technology integration, and environmental sustainability. With its ability to automate the folding and gluing process, this innovative machine ensures increased production rates, consistent box quality, and reduced labor costs. As packaging companies strive to provide efficient solutions that meet customers' evolving needs, the lock bottom folder gluer machine proves to be an indispensable tool in their operations. Embracing this cutting-edge technology enables companies to gain a competitive edge in the dynamic packaging industry, setting new benchmarks for packaging quality and efficiency.
Efficient and Versatile Semi-Automatic Thermal Film Laminating Machine for Enhanced Productivity
Title: Innovative Semi-Automatic Thermal Film Laminating Machine Introduces Enhanced Efficiency in the Printing IndustryIntroductionIn the era of modern printing technology, achieving efficient and high-quality laminating processes is crucial for businesses looking to stay competitive. One company has taken this challenge head-on by developing a cutting-edge semi-automatic thermal film laminating machine. By combining advanced features and ease of use, this machine promises to revolutionize the laminating process, offering improved productivity and cost-effectiveness to businesses in the printing industry.Machine OverviewThe semi-automatic thermal film laminating machine, developed by a leading machinery manufacturer (name withheld), boasts a range of innovative features that set it apart from traditional laminating machines. Engineered with user satisfaction in mind, this machine offers enhanced efficiency, durability, and convenience, making it the ideal choice for businesses of all sizes.Efficiency and Productivity BoostOne of the standout features of this new laminating machine is its streamlined semi-automatic operation. This design minimizes the need for constant manual interventions, allowing the laminating process to run smoothly with minimal supervision. This enhanced efficiency optimizes productivity, freeing up valuable time for operators to focus on other important tasks.With a sleek and ergonomic interface, the machine provides intuitive controls, ensuring ease of use for operators of all skill levels. Additionally, an integrated touch screen display allows users to monitor and adjust parameters such as temperature, speed, and pressure, catering to specific laminating requirements.Superior Quality LaminationEnsuring high-quality laminations is a top priority for businesses in the printing industry. This semi-automatic machine guarantees excellent results through its state-of-the-art heating system. Equipped with a precision heating element, it ensures even and consistent distribution of heat, eliminating the risk of bubbles or wrinkles in the laminated material. This feature enables businesses to achieve professional-looking outputs that meet the highest industry standards.Versatile and ReliableThe semi-automatic thermal film laminating machine has been designed to accommodate a wide range of laminate materials, making it versatile for various printing applications. Whether working with glossy, matte, or even textured films, this machine handles them all with precision and ease.Additionally, this innovative machine boasts a robust build, ensuring longevity and reliability in the demanding printing industry. Its heavy-duty construction provides stability during operation, reducing the risk of errors and damage to both the machine and the laminated material.Environmentally Friendly DesignIn today's eco-conscious world, businesses are increasingly seeking sustainable solutions. The semi-automatic thermal film laminating machine aligns with this trend by incorporating eco-friendly features. By utilizing energy-efficient heating elements and reducing the consumption of laminating films, this machine minimizes waste and environmental impact, providing a more sustainable option for businesses.ConclusionWith its combination of enhanced efficiency, exceptional quality, and user-friendly features, the semi-automatic thermal film laminating machine promises to revolutionize the printing industry and set new standards in laminating technology. By streamlining the laminating process, businesses can look forward to significant improvements in productivity and cost-effectiveness, ultimately enhancing their competitiveness in the market. With a commitment to sustainability and long-lasting performance, this machine exemplifies the continuous innovation within the printing industry.
Revolutionary Electric Laminating Machine That Alternates Heat and Cold Settings Now Available
Hot And Cold Electric Laminating Machine: The Innovative Solution for All Your Lamination NeedsIn today's world, where everyone is looking for ways to improve the durability and quality of their documents, posters, and other paper materials, laminating machines have become increasingly popular. Laminate sheets provide a protective layer to the material, making it resistant to wear and tear, water, and other elements. However, finding a reliable and efficient laminating machine that can cater to all your lamination needs can be a daunting task.With a focus on innovation and customer satisfaction, [Company Name] has launched an advanced hot and cold electric laminating machine that offers an unparalleled lamination experience. This laminator is designed to provide smooth and fast lamination for all types of paper materials, including cards, labels, posters, and documents.The hot and cold electric laminating machine incorporates advanced technology and features that make it a popular choice for both personal and professional use. This machine is perfect for home, office and business use and can cater to the lamination needs of individuals, schools, libraries, and large corporations.The hot and cold electric laminating machine is equipped with two modes of operation – hot and cold. The hot mode is ideal for use with only thermal laminating pouches, while the cold mode can be used for both thermal and self-adhesive pouches. This means that you can use a variety of laminating sheets with the machine. So, whether you want to laminate a document, business card, or a poster, this machine has got you covered.One of the standout features of this device is its speed. The hot and cold electric laminating machine is engineered to laminate papers quickly and efficiently, reducing the time needed for lamination. With a maximum lamination speed of up to 250mm/min, this machine can laminate a single A4 sheet in less than a minute. Whether you are dealing with bulk lamination or a small number of documents, this machine gets the job done in record time.Another significant advantage of this laminating machine is its versatility. The machine is designed to handle various paper sizes, including A4, A5, and A6 paper sizes. It is also compatible with thin and thick laminating pouches, ranging from 160 to 250 microns in thickness. This means that you can use it for different kinds of papers, with different thicknesses.Safety is another crucial aspect of this laminating machine. The machine is equipped with adequate safety feature, including automatic shut off. Additionally, the device has been designed with built-in air vents to prevent overheating during operation. As a result, the laminating machine remains safe during usage, giving you peace of mind.The hot and cold electric laminating machine has a simple and compact design, making it easy to store when not in use. Its lightweight and appropriate size make it easy to move, and it requires minimal storage space. The device is easy to use, even for beginners, and it comes with an instruction manual to guide you through the laminating process.In conclusion, the hot and cold electric laminating machine from [Company Name] is an ideal solution for all your lamination needs. It is fast, efficient, versatile, safe, and easy to use, making it a perfect choice for both personal and professional use. Purchase this laminating machine today and begin experiencing high-quality lamination results that will make your documents, posters, and other paper materials more durable and professional-looking.